CROC experts shared the main trends in the field of automation of logistics processes in retail and FMCG. In our opinion, these trends will affect not only a specific sector, but will affect all Russian companies. We recommend reading all the way to the end!
IT infrastructure localization
The first issue that retail market players will have to address in terms of IT is infrastructure localization. More and more foreign vendors are leaving Russia and the issue of business process continuity arises. The issue is most acute for large businesses that worked according to the standards of their foreign headquarters and built full-fledged ecosystems around Western systems. Nevertheless, retailers are in no hurry to migrate immediately and completely to Russian technologies – this requires significant investments, for which most businesses are not yet ready.
“As our experience shows, it is not necessary to change all systems at once and reshape the IT landscape; a compromise is acceptable between what must be localized and what can be left with local support. To find this compromise and minimize the risks that arise in the transition process (data loss, performance degradation, incompatibility of information systems), technology partners who have an understanding of the specifics of the retail industry help to find this compromise and minimize the risks that arise in the transition process (data loss, performance degradation, incompatibility of information systems). Such a partner acts as a supermarket of IT solutions from different vendors, from which it assembles a new sustainable digital ecosystem that meets the needs of the business”, – says Dmitry Smirnov, Director of Business Development in Retail and FMCG of the IT company CROC.
Transportation management automation
Changes in market conditions have affected the situation with transportation logistics in retail in a bad way: with the growth of online sales, logistics chains have become more complicated. Companies that used to do without automation will not be able to compete effectively in the market in the new conditions, because it is delivery problems that become an obstacle to business growth. The implementation of transport logistics automation systems helps to reduce routine processes and minimize losses associated with manual management.
“Due to properly structured logistics processes, retailers reduce operating costs and can compete more effectively in the price field. In 2023, when consumer demand is shrinking in the market, and the issue of even minimal savings becomes important for the consumer. Therefore, the ability to offer lower cost of goods to the customer is of particular importance to the business. In segments where margins are not very high, this is a determining factor”, – Nikita Kostenchuk, logistics expert at CROC IT company, explains.
Digital Warehouse
In recent years, the demand for process automation has been steadily increasing from warehouse owners. First and foremost, companies seek to increase warehouse turnover, improve customer service and reduce the number of claims on the quality of picking, optimize storage and inventory traceability. And if a company plans to scale up, expand its product range, a multiple growth of task volumes is inevitable. That is why the entry of trade to a new qualitative level is impossible without the development of warehouse infrastructure and logistics. Experts estimate that the introduction of “digital” in warehouse management reduces the company’s costs by more than 10% in total.
“Automated warehouse management systems facilitate the daily planning and control of warehouse resource utilization, movement and storage of products in and out of the warehouse. In addition, the training and onboarding time for new personnel is significantly reduced because the system thinks for the employee and prompts him or her for each subsequent action,” – Viktor Azyamov, an expert on implementation of logistics solutions of CROC IT company, explains.
Control of availability of goods on the shelves
Large retail chains face lack of goods on the shelf due to difficulties with logistics, display or merchandising management. The problem persists because in many companies, the process is still done manually. The task of automating merchandising needs to be tackled holistically, with the help of digital tools.
“Retailers lose hundreds of millions annually due to lack of goods on the shelf. The reasons are trivial – inaccurate inventory, irregular replenishment of stock, incorrect shelf monitoring. This creates a vicious cycle between logisticians, merchandisers, purchasing staff and suppliers who expect each other to solve the problem. Digital monitoring systems on the market today can identify the objective causes of shortages by automatically retraining algorithms based on feedback from store employees. This approach leads to significant cost reductions.” – Dmitry Smirnov comments .
Demand forecasting and sales planning
When planning sales, companies first analyze and consider consumer demand. Modern IT systems for demand forecasting help retailers and manufacturers meet this challenge. Purchases, delivery schedules, transportation and other operations are planned based on historical data collection and calculations. The same forecast is used to calculate how much inventory to keep in stock so that there is no surplus or shortage.
“Russian retailers incur heavy losses when calculations are done manually in Excel. According to our calculations, automating the process using specialized solutions can improve planning accuracy by up to 20%, and planning labor costs are reduced by 2-4 times,” says Dmitry Smirnov .
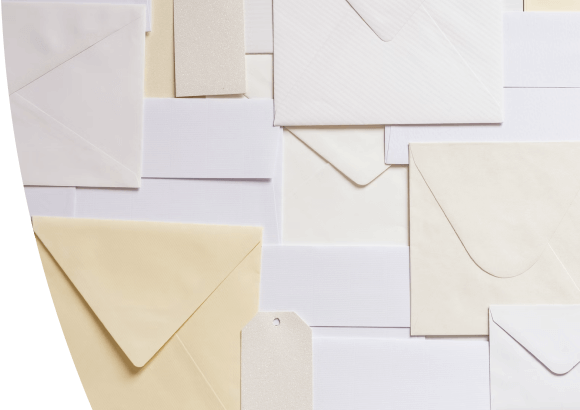
Would you like to receive a selection of articles in the mail?
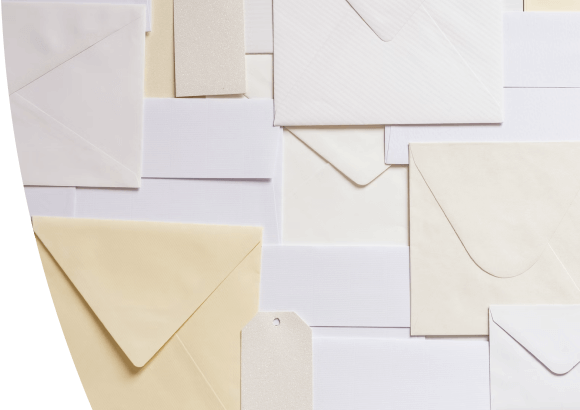